Fits following cars:
Suitable for original anti-roll bar with flattening. Not suitable for MPS.
- Ford C-Max - DM2: All [2007-2010]
- Ford Focus - LS, LT, LV: w/o RS/ST [2005-2011]
- Ford Focus - DA_, FFS, DS, HCP, DP: w/o RS/ST [2004-2012]
- Ford Kuga - All [2008-2012]
- Ford Tourneo Connect - All Connect Models (Series 2) [2013-2020]
- Ford Transit Connect - All Connect Models (Series 2) [2013->]
- Mazda 3 - BL: All [2008-2014]
- Mazda 3 - BK: w/o MPS [2000-2009]
- Mazda 5 - CR19: All [2005-2010]
- Volvo C30 - 533: Mk I [2006-2012]
What are SuperPro Polyurethane Suspension Bushes?
SuperPro chassis bushings replace the original rubber mounts, e.g. in the wishbones, which wear out quickly due to the susceptibility of the rubber material to environmental influences. Polyurethane, on the other hand, offers a much longer service life and improves, among other things, the handling and driving experience in curves, since SuperPro bushings are a specially reinforced material that is also used in motorsport. Furthermore, the bearings are particularly useful when replacing the worn original bearings, since SuperPro bearings are usually cheaper than original bearings.
In which applications are SuperPro chassis bushes used?
SuperPro products are specifically used for vehicles driven in extreme situations. However, polyurethane bushings can also be used in normal road vehicles. Original rubber bearings wear out very quickly (cracks, etc.), which means that they have to be replaced. Since the original bearings are usually more expensive than SuperPro products, it makes sense to switch to SuperPro polyurethane bushings and thus improve handling. The installation effort here is exactly the same as with original rubber bearings.
SuperPro sockets are primarily designed for the following areas of application:
- hill climb
- drifting
- Off-road & 4x4
- Racing
- Rally
- Circuit driving
- Spring & Hill Climbs
- fast cornering
Replacing the original rubber chassis bushings has the following advantages:
- more precise steering behavior
- better handling
- more traction
- Longevity
- lower tire wear
SuperPro products are constantly tested under the toughest conditions. Furthermore, the factory has special test equipment to subject the bushings to even higher loads and also to test their longevity.
SuperPro is the most technologically advanced landing gear bushing - what are the reasons for this?
The SuperPro polyurethane material is based on a polyether. The material from other manufacturers is based on polyester, which has a very high water content. Due to the effects of force and temperature changes, this water content decreases steadily and leads to hardening of the bush and ultimately to crumbling of the material. As a result, the vehicle's "hard feel" steadily increases over time, making driving increasingly uncomfortable. Polyether-based polyurethane, on the other hand, has a fundamentally different chemical structure and is therefore more resistant to all environmental influences.
- SuperPro Clear Grease has been specially formulated for use with SuperPro Polyurethane material and is based on a silicone which protects the grease from drying out ensuring long bushing life.
- The helical knurling in the bore of the bush also ensures that the grease stays there and lubrication is ensured for a long time. In addition, this transports the excess grease to the outside when the bolt is pressed in and thus keeps the correct amount in the bush.
- The metal bolt is pressed firmly into the sockets (e.g. with a vise or press) to enable an even tighter fit and thus better driving characteristics. With most sockets from other manufacturers, the metal bolts can be pushed into the socket very easily by hand.
- Many customers ask about the Shore hardness of the bushings. Due to the fact that the metal bolt (see previous point) is pressed firmly into the bushing, this degree of hardness is not decisive, as this will make the bushing even stronger. As a result, you can't make a comparison to competing products based on this value. All degrees of hardness have been optimally adjusted in extensive driving and laboratory tests for each vehicle type and each installation position. If you purchase a complete set, each socket may have a different hardness in order to ensure optimal performance in combination.
- Most (wishbone) bushings have a metal shell (like original bushings) around the bushing, which other manufacturers do not have. This gives the bushing extra strength and a better fit under load than solid polyurethane bushings. Furthermore, there is no direct contact between the polyurethane and the handlebars, so that thanks to the metal shell no lubrication is necessary and therefore no squeaking noises can develop.
- SuperPro bushings are not a simple "polyurethane block" machined to the shape of the original bushings. The degree of hardness of each individual socket on the vehicle is adjusted separately. Furthermore, polyurethane in chassis technology often requires a fundamentally different design than rubber bushings. This is especially the case on newer vehicles where the bushing technology is more advanced.
Let's take bushings for the rigid axle on the rear axle as an example - despite the different material properties compared to rubber, the pivoting of the axle must be guaranteed. So it is not enough to just make a simple replacement for the rubber bushings in polyurethane, but rather to develop and extensively test a complex design in order to ensure the same pivoting of the axle with better driving characteristics.
advantages in detail
polyurethane
The special SuperPro polyurethane mixture has specific mechanical properties that are particularly advantageous when used in chassis technology. Extreme abrasion resistance, low compression set, high tear strength, and resistance to oils and solvents make SuperPro ideal for most automotive applications. Exactly these features result in an elastic product that is very versatile in its various applications. Thanks to the material and design technologies used in the manufacture of SuperPro bushings, they will not introduce increased noise, vibration or harshness (GVH) compared to standard rubber bushings.
metal studs
The metal bolt is a significant component of the landing gear bushing that allows the handlebars to remain free to pivot. The production of the bolts is subject to the highest precision to ensure an exact fit. All SuperPro bolts are also made from galvanized steel to protect against corrosion. It is in no way necessary to manufacture it from stainless steel, since the outside of the bolt comes into contact with the bushing, the surface of which is wetted with grease during installation. The bolt lies directly against the stops, so that no water can penetrate here. Long-term tests have shown that no corrosion occurs even after years.
If the application calls for it, SuperPro also offers precision-machined bushings with zinc-plated metal shells into which the polyurethane is poured. The structure of the bushing is therefore exactly like the original rubber bushings, which ensures a tight fit in the handlebars. Because there is no direct contact between the handlebar and the polyurethane, these bushings are completely maintenance-free.
The double helix
The double helix skeleton incorporated into the bushings has led to far-reaching improvements in SuperPro products. This system can be found inside the bushing, the surface of which will later come into contact with the bolt.
The double helix design was used on all bushings, whether wishbone or stabilizer bushings, to distribute the lubricating grease perfectly on the surface and thus ensure long-term lubrication. This allows the grease to be evenly distributed and completely coat the surface of the pin as it is pressed into the bushing. In addition, this structure reduces the contact area of the bolt with the polyurethane, resulting in no noise. Thanks to the helical structure, excess fat is also cleanly transported to the outside when pressed in.
Bullet-shaped grooves
The bullet shaped grooves are also an important part of the design of SuperPro polyurethane bushings. These are arranged at equal intervals on the outer surface of the bushings and compensate for small deviations in the diameter of the wishbone mount. In this way, manufacturing tolerances, which occur particularly with handlebars and chassis parts from accessories, can be compensated.
SuperPro Polyurethane has a solid, rigid shape after machining, but under load it behaves like a kind of displaceable liquid thanks to its unique properties. Exactly this displacement also takes place, for example, when cornering at high speed. The grooves prevent the generation of noise and the transmission of vibrations, since the polyurethane can expand into the bulges.
Tangential grooves in the head area
The tangentially tapering grease grooves in the head area of shackle bushings reduce the friction of the bushing head at the stop. The grooves "store" grease, which constantly lubricates the surface during turning operations. This leads to less friction of the socket head and also reduces noise.
Research and Development
The complex research and development process of SuperPro products always brings new innovations with it. That is why SuperPro products are constantly being provided with new features and further developed. The tests are not only carried out in the laboratory but mainly in the installed state in vehicles. The vehicles are driven in different climate zones (Africa, Asia, Australia, Europe, Middle East, South Pacific and USA) to test the effects of extreme temperatures. Of course, the practical tests mostly include circuit drives, because this is where the greatest forces occur.
Tests in the laboratory, in which the bushings are subjected to heavy loads over a long period of time, show the long durability and resilience of SuperPro products.
Driving comfort paired with better road holding - the SuperPro polyurethane material makes it possible
Nowadays there are many prejudices against polyurethane in chassis technology: PU bushings would make the driving feel "hard", noise would develop or cause increased vibrations. But you have to differentiate correctly, because one polyurethane is not the same as the other! Depending on the chemical composition, the respective polyurethane mixture also has fundamentally different properties. In the chassis technology, SuperPro uses a very high-quality polyether-polyurethane, which, in contrast to the polyester-polyurethane of other manufacturers, is fundamentally different in terms of its chemical structure and therefore also has different properties.
Differences between polyurethane materials
The following chart shows the differences between SuperPro's polyether-polyurethane and competitor's polyester-polyurethane:
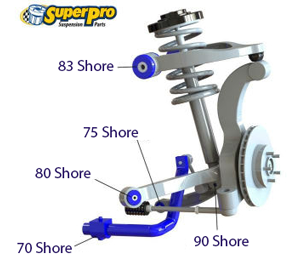
Properties of the SuperPro polyether polyurethane material
As you can see, the SuperPro polyether-polyurethane has a progressive property. This means that the more force acts on the bush, the more counterforce the bush also develops (resilience). As a result, when a slight force is applied to the bushing (e.g. uneven floors), only a small counterforce is obtained, which means that these forces are taken up and absorbed by the bushing. In this case, the driver drives just as comfortably as with the original rubber bushings! However, if the SuperPro bushing experiences a strong impact (e.g. when cornering quickly or on the race track), it reacts with a high restoring force, which leads to direct steering behavior.
Conclusion: Depending on the situation, the SuperPro socket reacts differently. With our products we guarantee the comfort of rubber but at the same time the handling of a very hard material.
Polyester polyurethane material from many other landing gear bushing manufacturers
From the diagram it can be seen that the polyester-polyurethane has a fundamentally different character than the SuperPro polyether-polyurethane material. You will look in vain for the progressive quality here. This material reacts almost always with the same force, no matter how high the force acting on the bushing is. This inevitably results in hard driving!
Degree of hardness of the polyurethane material
Many customers ask about the hardness of the polyurethane material used. There is no general answer to this, as the degree of hardness of each individual bushing on a vehicle is individually adjusted by our engineers in extensive road tests according to the force acting on the respective installation position.
Other manufacturers use the same degree of hardness across all sockets on the vehicle. In SuperPro's opinion, this does not make sense, since a different force acts on each bushing in the vehicle. As a rule, the most heavily loaded bushing is the rear bushing of the lower control arm on the front axle. SuperPro usually also offers different degrees of hardness for this bushing - usually 70 or 80 shore for the road and 90 shore in motorsport. However, this is more due to the durability of a harder material at high forces than to better handling. This is due to the progressive nature of the SuperPro polyurethane material, as described in the first section.
The bushings on the rear axle, on the other hand, are far less stressed, which means that the degree of hardness must be different to that of the front axle, depending on the position. This is the only way to ensure the same "dynamic" degrees of hardness on the front and rear axles or all installation positions.
In addition to the individually tuned degrees of hardness, the bore in the bushing is slightly smaller than the diameter of the sleeve, which means that the bushing increases in strength after the sleeve is pressed in. In the diagram above, the curve therefore starts above the zero point, as there is already a small amount of preload which holds the bushing firmly in the handlebars after the sleeve has been pressed in.
SuperPro avoids NVH (noise, vibration, harshness) thanks to the special polyurethane material and individually adjusted degrees of hardness
With the special material and the degrees of hardness that are tailored to the installation position, SuperPro ensures that the driving comfort corresponds to that of original rubber bushes, but the sporty driving behavior corresponds to that of a very hard material, even when installing a complete bushing kit.